What to Look for in a Reliable Fleet Maintenance Provider
Look for deep diesel expertise, mobile service, transparent pricing, strong warranties, and compliance knowledge when choosing a fleet maintenance provider.
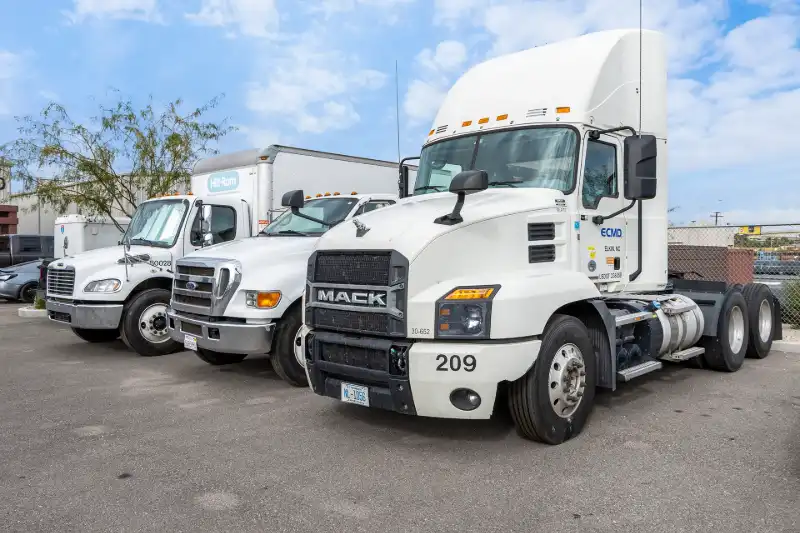
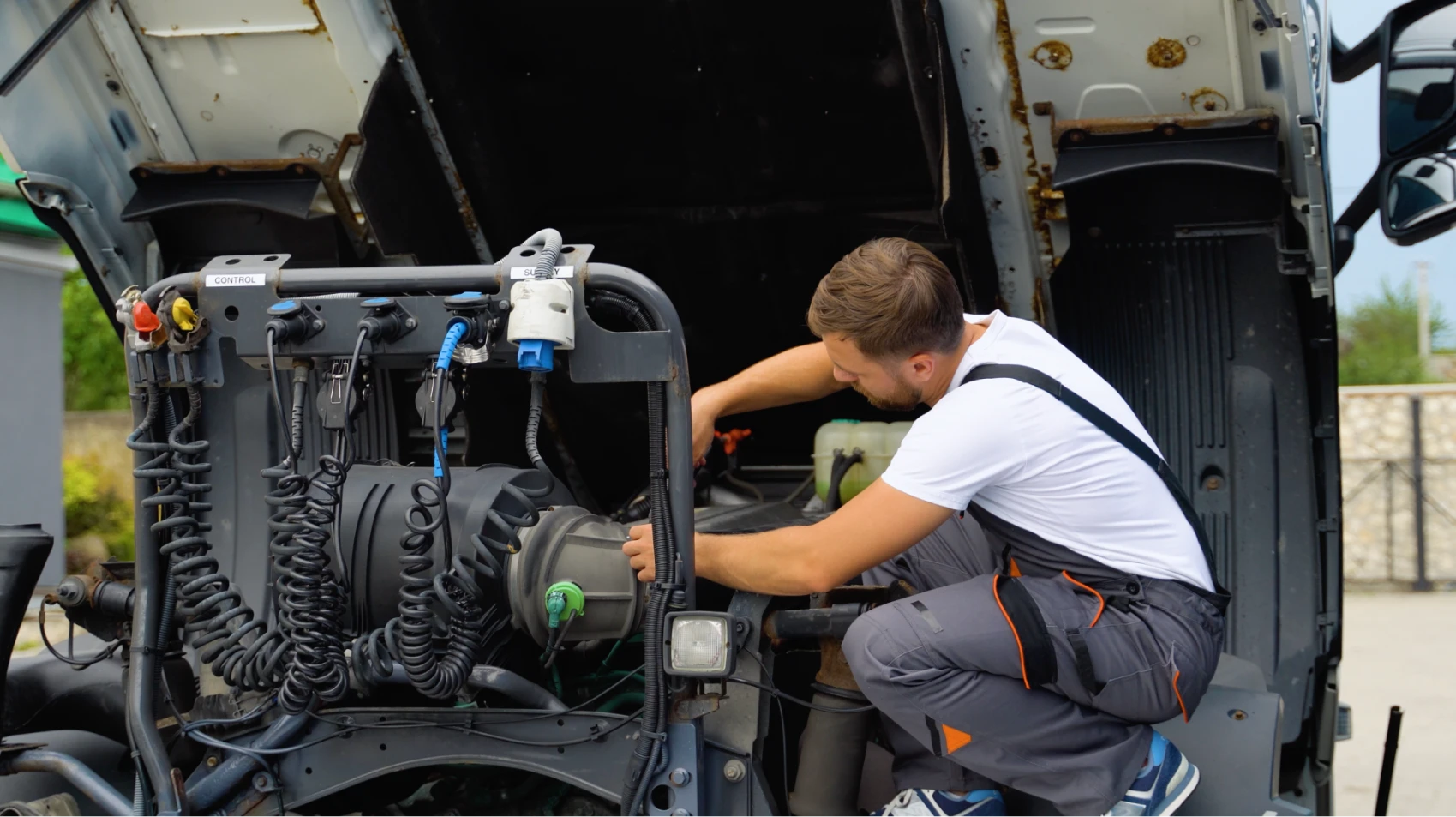
Keeping your fleet road-ready is about safety, uptime, and the bottom line. When one truck is down, your whole operation can feel it, especially for owner operators. That’s why finding a reliable fleet maintenance provider isn’t just a smart move—it’s essential. But with so many shops promising the moon, how do you separate the real deal from the smoke and mirrors?
Let’s break down what to look for, what to avoid, and how to make a choice that keeps your trucks and business rolling smoothly.
Proven Experience with Heavy-Duty Equipment
Diesel trucks aren’t your average pickup. They’ve got complex systems, specialized parts, and they work hard day in and day out. A quality provider should have deep expertise in diesel engines, transmissions, and after-treatment systems.
From EGR and DPF cleaning to transmission rebuilds and air brake systems, your provider should know it like the back of their calloused hand. Ask how long they’ve been in business, whether their techs are ASE-certified, and if they’ve got hands-on experience with your fleet’s exact makes and models.
Preventive Maintenance Program
If your provider still reacts to breakdowns, they’re behind the times. A true partner in fleet care should offer a robust preventive maintenance plan, built around your vehicles’ usage, mileage, and duty cycles. Preventive maintenance should reduce your emergency calls, not increase them.
- Regular oil and fluid checks should be scheduled based on engine hours or miles driven, not just a generic calendar reminder. Skipping these can lead to avoidable engine wear and overheating.
- Brake inspections are vital in preventing costly accidents and ensuring compliance. A reliable provider will monitor brake wear, slack adjuster settings, and drum condition.
- Suspension diagnostics should include visual inspections, ride height checks, and attention to leaf springs or airbag integrity—both of which directly affect handling and cargo stability.
- BIT Inspections every 90 days are a legal requirement in California but also a good best practice elsewhere. A solid provider won’t just “pass” your trucks—they’ll proactively fix what’s needed before it becomes a liability.
- ECM diagnostics for error codes and emissions compliance ensure your truck’s computer system is healthy, catching DEF faults, regen failures, and engine derates before they shut you down on the road.
Mobile Service Capabilities
Let’s be real—hauling a dozen trucks to the shop is a logistical nightmare. Mobile fleet maintenance means your techs come to you, whether it’s scheduled PM or mid-shift troubleshooting. A good mobile crew can handle about 80% of maintenance on-site, saving you time, fuel, and hassle.
- DOT Inspections can be performed on-site, minimizing downtime and keeping your team focused on their routes instead of shop runs.
- Fluid top-offs and filter swaps are quick tasks that can be done in your yard, keeping your trucks topped up and clean without pulling them off the road.
- Air system diagnostics can be handled right where the truck is parked, reducing brake-related risks before a road test is needed.
- Minor repairs and resets, like tightening belts, clearing ECM codes, or replacing sensors, save hours of downtime when done immediately in your yard instead of waiting in line at a shop.
Emergency Roadside Support
Things go wrong. When they do, you want someone on-call who knows your fleet. A dependable provider should offer 24/7 roadside assistance, not just a daytime tow service.
- Response time guarantees mean less time waiting on the shoulder and more time getting your load delivered. A fast response can prevent a minor issue from turning major.
- On-site diagnostics allow techs to scan codes, run voltage checks, and evaluate mechanical failures on the spot—without needing a tow.
- Common parts stocked on the service truck—like belts, sensors, or air lines—mean quick repairs and faster turnaround times.
- Strong communication with your dispatch team ensures everyone’s in the loop. This reduces confusion, overlaps, and keeps customers informed of delays.
Transparency in Pricing & Work Orders
Nobody likes surprise charges. Your provider should offer clear work orders, line-item pricing, and explain their recommendations without hiding behind jargon. Bonus points if they use a fleet management system that gives you access to all your trucks’ records in one place. A few points to keep in mind include:
- Upfront estimates help you plan your maintenance budget better and avoid being blindsided with inflated bills after the work is done.
- Easy-to-read invoices break down the labor, parts, and diagnostics separately so you can see where your money went—and where it didn’t.
- Digital inspection reports with photos add visual proof to service recommendations. A picture of a leaking hub seal or cracked brake lining speaks louder than a checklist.
- Documentation of replaced parts keeps your fleet history clean and helps you anticipate future maintenance cycles with real data.
Quality Parts & Warranty Coverage
Even the best wrench turners can’t make up for lousy parts. Make sure your provider uses OEM or top-tier aftermarket components and backs their work with a clear warranty. If they’re cutting corners here, your uptime will pay the price later. Look for one of the following for quality repair shops:
- Parts AND labor coverage gives you full peace of mind. No one wants to pay twice for a bad install or defective sensor.
- Workmanship warranties on diagnostics and repairs prove the provider stands behind their skill—not just the parts.
Minimum 90-day coverage for standard repairs, and longer on major rebuilds, should be your baseline expectation.
Compliance Knowledge
Emissions system regulations require shops to monitor regen cycles, DEF levels, and after-treatment health to avoid derates or fines. From SCR systems to DEF monitoring, compliance is more complicated than ever. Your provider must stay current on all relevant regulations. A provider that knows these inside out will catch what auditors will. This includes DOT inspection protocols, like brake stroke measurements and lighting systems. Having a good grasp of record keeping and Data logging supports audits and can help you contest violations with clear evidence of compliance.
Local Reputation & Fleet References
Word of mouth is gold. A well-established provider should have references from other fleet operators who’ll vouch for their consistency, professionalism, and results. Here are some ways you can learn about a shop’s reputation:
- Online reviews from fleet customers show you how they treat multi-unit operations, not just walk-ins with one truck.
- Case studies or testimonials should reflect real results—lower downtime, extended service intervals, or reduced compliance violations.
- Before-and-after documentation shows exactly what was fixed and how it improved performance or reliability.
Choose the Right Fleet Maintenance Provider Today
Choosing a reliable fleet maintenance provider isn’t just about grease guns and wrenches—it’s about partnership, planning, and protecting your uptime. From in-depth diesel-specific experience to mobile maintenance, transparency, and compliance know-how, every piece matters. The right provider won’t just fix problems—they’ll help you avoid them.
Ready to stop worrying about your fleet? D&J Diesel Fleet Service is a provider who checks every box and maybe even a few you didn’t know you needed. Our team helps your heavy-duty vehicles return to the road and stay on the road. Get in touch with us today or read our other article about preventive maintenance to learn more.
7:00 AM - 7:00 PM